
19 developed an epoxy-based ink that allows for the 3D printing of lightweight cellular composites with high aspect ratio microfibers that are aligned by the shear forces generated during the printing process. In a movement toward micro-reinforcement, Compton et al. In this work the length scale of the hard and soft phases are in the range of several millimetres. 18 provided a first attempt at using 3D printing to create tough composites inspired by bone to achieve a toughness modulus over 20 times that of its constituents. Randomized fibres (standard for systems without control) perform between these two extremes and negligibly affect composite strength while severely sacrificing ductility 17. Fibres aligned parallel to the predominant stresses reinforce the encompassing matrix, while orthogonal fibres act as defects, weakening the polymer matrix 15, 16. These precision printers are currently limited to reinforcement fibres with length scales greater than millimetres and geometries larger than centimeters with orientation control limited to the x– y plane.Īrguably the greatest challenge of adapting additive manufacturing technology to discontinuous fibre-reinforced composites is the ability to orient reinforcing fibres during the printing process 13, 14. Industrial-scale automated fibre placement printers have been developed that can print continuous strand carbon fibre-, Kevlar- and fiberglass-reinforced polymer 12. As printed polymers are lightweight but relatively weak, 3D printing is now moving toward manufacturing fibre-reinforced polymer composites owing to their impressive strength-to-weight ratios 11.
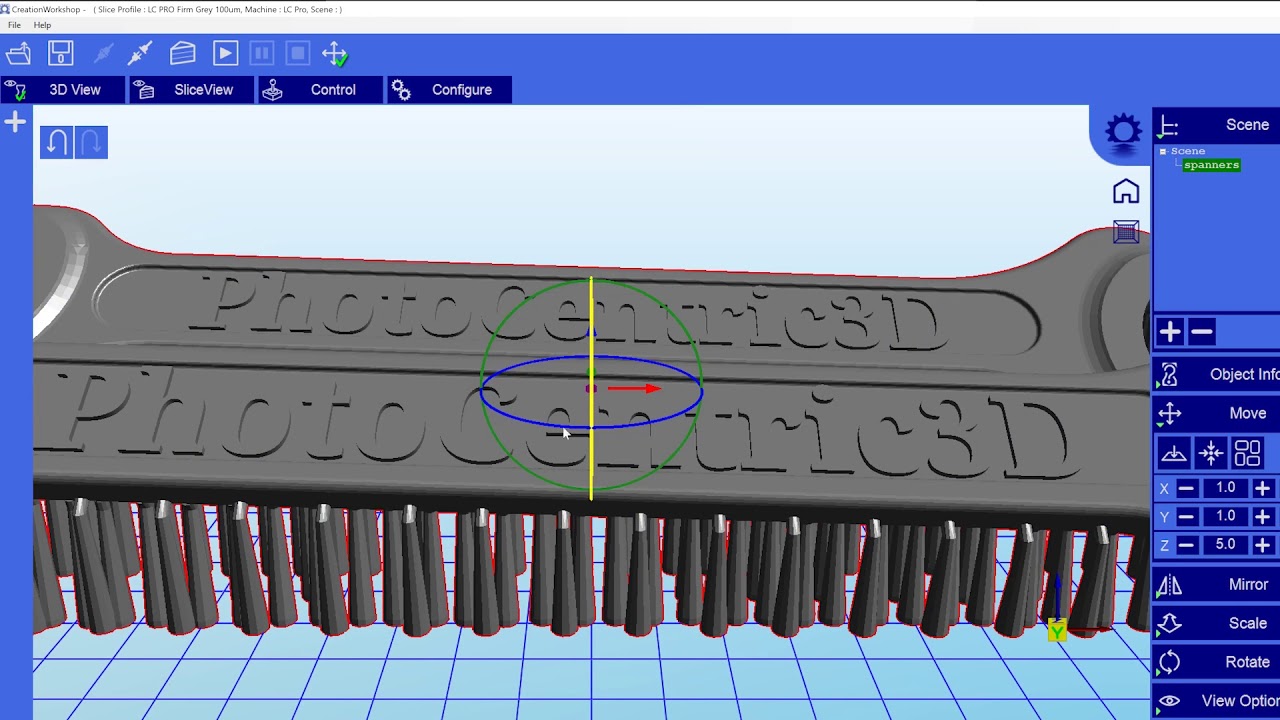
3D printing represents one of the most effective ways to manufacture customized parts with significant complexity which explains its ubiquity in industry, academia and personal use 10. The printing of polymers has been accomplished mainly by extrusion-based methods for thermoplastics and stereolithography (SLA)-based photo-polymerization for both thermoplastics and thermosets 5. These structures have voxel resolution down to tens of microns and have been used to print load-bearing mechanical structures from gears to functional fuel nozzles for jet engines 9. Though natural manufacturing processes are complex, novel colloidal assembly techniques and advances in additive manufacturing can be harnessed to also grow synthetic composites with similarly complex architectures.Īdditive manufacturing (three-dimensional (3D) printing) offers a very effective platform for generating complex 3D architectures out of a variety of materials from polymers 5 to metals 6, 7 to ceramics 8. Reinforcement architectures in synthetic composites are currently limited, in part, by our inability to control the local orientation of the stiff elements that comprise the reinforcement architecture. The diversity of reinforcement architectures in natural materials far exceeds the composite design currently available in synthetic materials. Such ordered, yet heterogeneous, reinforcement architectures are frequently linked to superior mechanical properties. To grow these reinforcement architectures, biological systems invoke complex cellular and molecular processes. Natural composites utilize reinforcing particles exquisitely organized into complex architectures to achieve superior mechanical properties including the shells of abalones 1, the dactyl clubs of peacock mantis shrimp 2, 3 and the cortical bones of mammals 4. Further, we demonstrate that we can now design and evolve elaborate reinforcement architectures that are not found in nature, demonstrating a high level of possible customization in discontinuous fibre composites with arbitrary geometries.
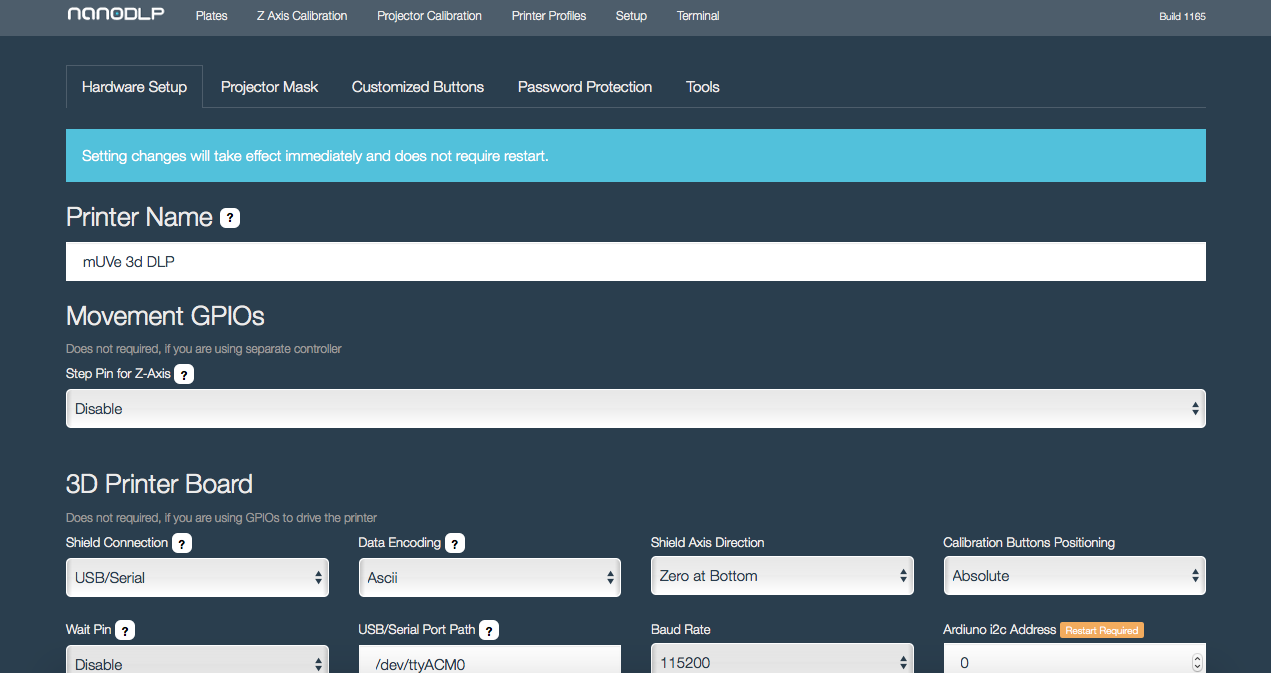
This technology, termed as ‘3D magnetic printing’, has enabled us to recreate complex bioinspired reinforcement architectures that deliver enhanced material performance compared with monolithic structures. Here we present an additive manufacturing approach that combines real-time colloidal assembly with existing additive manufacturing technologies to create highly programmable discontinuous fibre composites.
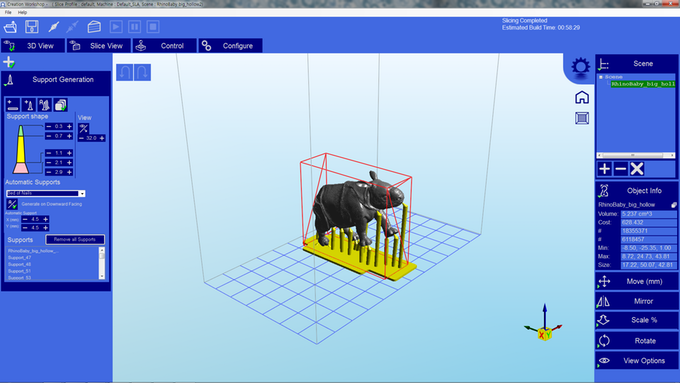
Many natural structures out-perform the conventional synthetic counterparts due, in part, to the more elaborate reinforcement architectures that occur in natural composites. These advantages partially explain the abundance and variety of discontinuous fibre composites that have evolved in the natural world. Discontinuous fibre composites represent a class of materials that are strong, lightweight and have remarkable fracture toughness.
